Researcher part of project aimed at producing third-generation biofuels from microalgae in Germany
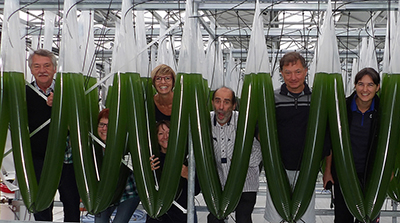
Some of the researchers and technicians among the tubes of the Novagreen bioreactor (Prof Grobbelaar on left)
|
A researcher from the University of the Free State (UFS), Prof Johan Grobbelaar, was invited to join a group of scientists recently at the Institute for Bio- and Geo-Sciences of the Research Centre Jülich, in Germany, where microalgae are used for lipid (oil) production, and then converted to kerosene for the aviation industry.
The project is probably the first of its kind to address bio-fuel production from microalgae on such a large scale.
“The potential of algae as a fuel source is undisputed, because it was these photoautotrophic micro-organisms that were fixing sunlight energy into lipids for millions of years, generating the petroleum reserves that modern human civilisation uses today. However, these reserves are finite, so the challenge is marrying biology with technology to produce economically-competitive fuels without harming the environment and compromising our food security. The fundamental ability that microalgae have to produce energy-rich biomass from CO2, nutrients, and sunlight through photosynthesis for biofuels, is commonly referred to as the Third-Generation Biofuels (3G),” said Prof Grobbelaar.
The key compounds used for bio-diesel and kerosene production are the lipids and, more particularly, the triacylglyserols commonly referred to as TAGs. These lipids, once extracted, need to be trans-esterified for biodiesel, while a further “cracking” step is required to produce kerosene. Microalgae can store energy as lipids and/or carbohydrates. However, for biofuels, microalgae with high TAG contents are required. A number of such algae have been isolated, and lipid contents of up to 60% have been achieved.
According to Prof Grobbelaar, the challenge is large-scale, high-volume production, since it is easy to manipulate growth conditions in the laboratory for experimental purposes.
The AUFWIND project (AUFWIND, a German term for up-current, or new impetus) in Germany consists of three different commercially-available photobioreactor types, which are being compared for lipid production.
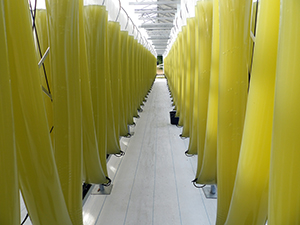
Manipulated Chlorella with high lipid contents (yellow) in the Novagreen bioreactor |
The photobioreactors each occupies 500 m2 of land surface area, are situated next to one another, and can be monitored continuously. The three systems are from Novagreen, IGV, and Phytolutions. The Novagreen photobioreactor is housed in a glass house, and consist of interconnected vertical plastic tubes roughly 150 mm in diameter. The Phytolutions system is outdoors, and consists of curtains of vertical plastic tubes with a diameter of about 90 mm. The most ambitious photobioreactor is from IGV, and consists of horizontally-layered nets housed in a plastic growth hall, where the algae are sprayed over the nets, and allowed to grow while dripping from one net to the next.
Prof Grobbelaar’s main task was to manipulate growth conditions in such a way that the microalgae converted their stored energy into lipids, and to establish protocols to run the various photobioreactors. This was accomplished in just over two months of intensive experimentation, and included modifications to the designs of the photobioreactors, the microalgal strain selection, and the replacement of the nutrient broth with a so-called balanced one.
Prof Grobbelaar has no illusions regarding the economic feasibility of the project. However, with continued research, optimisation, and utilisation of waste resources, it is highly likely that the first long-haul flights using microalgal-derived kerosene will be possible in the not-too-distant future.
Prof Grobbelaar from the Department of Plant Sciences, although partly retired, still serves on the editorial boards of several journals. He is also involved with the examining of PhDs, many of them from abroad. In addition, he assisted the Technology Innovation Agency of South Africa in the formulation of an algae-biotechnology and training centre. “The chances are good that such a centre will be established in Upington, in the Northern Cape,” Prof Grobbelaar said.