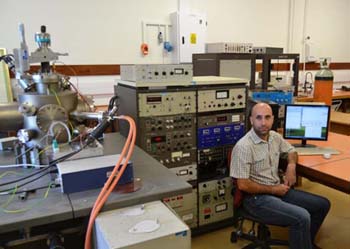
Shaun Cronjé, a PhD student, in a surface characterisation laboratory at the UFS. |
It is well known that the surface of a component is much more vulnerable to damage than the interior, and that surface-originated degradation such as wear, corrosion, and fracture will eventually destroy the component.
“Engineering the surface, based on scientific knowledge, is essential to control these damaging processes. It also creates electronic and geometric structures on the surface which opens up a world of new devices, especially considering the properties on the nano-length scale,” said Prof Wiets Roos from the Department of Physics at the University of the Free State (UFS).
At elevated temperatures, atoms are more mobile and can migrate to grain boundaries and surfaces, which have a major influence on material properties. The redistribution of solute atoms between the surface and the bulk of the material is known as segregation. Knowing the behaviour of segregation at the surface/environment interface can be very useful in the development of new materials. As an example materials can be improved higher efficiency and lower fuel consumption, thus reducing environmental pollution.
The main aims of Prof Roos’s research are to understand surface segregation, use it as a tool, and contribute to the various surface engineering fields.
The surface characterisation laboratories at the UFS are well equipped to do high temperature segregation measurements, and have already proven a success, not only in the ability to prepare the specimens for characterisation, but also in developing models and procedures to quantify the segregation parameters.
The most recent results have demonstrated the importance of taking evaporation into account during quantification.” This has laid the foundation for future studies by installing the necessary hardware in a surface characterisation spectrometer, establishing experimental protocols, and improving an existing model (developed in this laboratory) for simulating segregation profiles,” said Prof Roos.
Segregation parameters allow the researcher to predict and utilise the surface concentration behaviour as a function of temperature and time. “This not only contributes to fields involving corrosion, oxidation, sintering, wear, chemical poisoning, powder metallurgy, and lubrication but adds to the development of self-healing devices,” said Prof Roos.