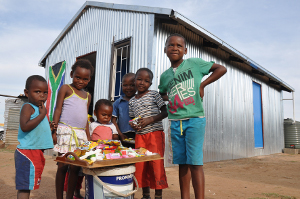
Photo: Stephen Collett |
When Prof Basie Verster, retired head of the Department of Quantity Surveying at the University of the Free State (UFS), initiated an alternative form of housing for Johannes - one of his employees - a decision was made to base research on this initiative. This research project in Grasslands, Heidedal focused on the cost and energy efficiency of green and/or sustainable shacks.
Esti Jacobs from the Department of Quantity Surveying, together with an honours student in Quantity Surveying, a master’s student in Architecture, and young professionals at Verster Berry, helped with the project.
The physical goals of the project were to create a structure that is environmentally friendly, and maintains a comfortable interior climate in winter and summer, as well as being cost-effective to erect. The structure also had to be socially acceptable to the family and the community.
“The intention was to make a positive contribution to the community and to initiate social upliftment through this project. Structures such as the ‘green shack’ may serve as an intermediate step to future housing possibilities, since these structures are relatively primitive, but have economic value and could be marketable,” she said.
Esti explains the structure of the building, which consists of gum poles and South African pine bearers, with a timber roof and internal cement block flooring. The building is clad with corrugated iron and has a corrugated iron roof finish. Additional green elements added to the structure were internal Nutec cladding, glasswool insulation in walls, internal gypsum ceiling boards with ‘Think Pink’ insulation, internal dividing wall and door, polystyrene in the floors, and tint on the windows. A small solar panel for limited electricity use (one or two lights and electricity to charge a cellphone) and a Jojo water tank for household consumption by the inhabitants were also installed.
Esti said: “Phase one of the research has been completed. This phase consisted of an investigation into the cost of an alternative form of housing structure (comparing traditional shacks with the planned structure) as well as the construction process of the physical housing structure.
“Phase two of the research, commencing in February 2015, will last for two to three years. This phase will include the installation of temperature and relative humidity logging devices inside the existing traditional shack and the new green shack. The logs will be regularly monitored by the UFS Department of Quantity Surveying and Construction Management.
These data will enable the researchers to measure the differences in comfort levels inside the two different structures. The data, together with other information such as building materials and methods, are then processed by software programs. Through the simulation of different environments, building materials, and alternate forms of energy, software models can be used to come up with conclusions regarding more energy-friendly building materials and methods. This knowledge can be used to improve comfort levels within smaller, low-cost housing units.
The UFS will be working with Prof Jeff Ramsdell of the Appalachian State University in the USA and his team on the second phase of the project.
“This research project is ongoing and will be completed only in a few years’ time,” said Esti.
The results of the research will be published in accredited journals or at international conferences.
For more information or enquiries contact news@ufs.ac.za.