Pure curiosity.
That was what gave rise to the development of a new textile, which was created in the Textile Lab and later evaluated for consumer use in the Sensory Lab of the University of the Free State (UFS).
Matseliso Monnapula, a master’s student in the
Division of Consumer Science, is experimenting with bacterial cellulose, which is produced as a by-product in the fermentation process when making kombucha. Her goal is to determine its efficacy as a possible sustainable textile alternative for use in the apparel industry.
She says finding this textile alternative was initially the result of pure curiosity. “My brother brews kombucha, so we always wondered in what other ways this fascinating mass of cellulose could be used.”
“It was upon further research that we discovered that there actually is more to it – from within the textile industry, biomedical and tissue engineering disciplines, paper and audio speaker manufacturing, to even the food industry,” states Monnapula.
The interesting process of growing this textile entails brewing tea (black, green, or rooibos tea can be used for this purpose) and adding sugar, vinegar, or previously brewed kombucha to maintain a favourable pH level. “One then inoculates the sweetened tea with a starter culture of acetic acid bacteria and yeasts, also known as SCOBY (symbiotic culture of bacteria and yeasts). It is then left for two to four weeks under specific conditions, during which the fermentation process takes place. In this period, the cellulose gradually starts to form on the liquid’s surface,” explains Monnapula, who was assisted by her co-supervisor, Prof Celia Hugo from the Department of Microbiology and Biochemistry.
Vegan leather
The process of making bacterial cellulose accounts for the many benefits of this leather-like textile. “The process and its aftermath are significantly less detrimental to the environment than most commercial textiles produced today. It is known that the textile industry is characterised by the excessive usage of chemicals, water, energy, and the generation of toxic effluent that is not always disposed of correctly, thereby affecting human, vegetal and animal well-being. Moreover, it eliminates animal cruelty, and in relation to real leather, it will also be more available and less expensive.”
“Secondly,” she states, “bacterial cellulose is biodegradable, which is one way of contributing towards a circular economy in the textile industry, while moving away from the traditional linear economy we know today.”
Within the apparel industry, this textile, which is mostly suitable for accessories, can be used to make products that are typically made of leather. For instance, bags, jackets, shoes, and bucket hats.
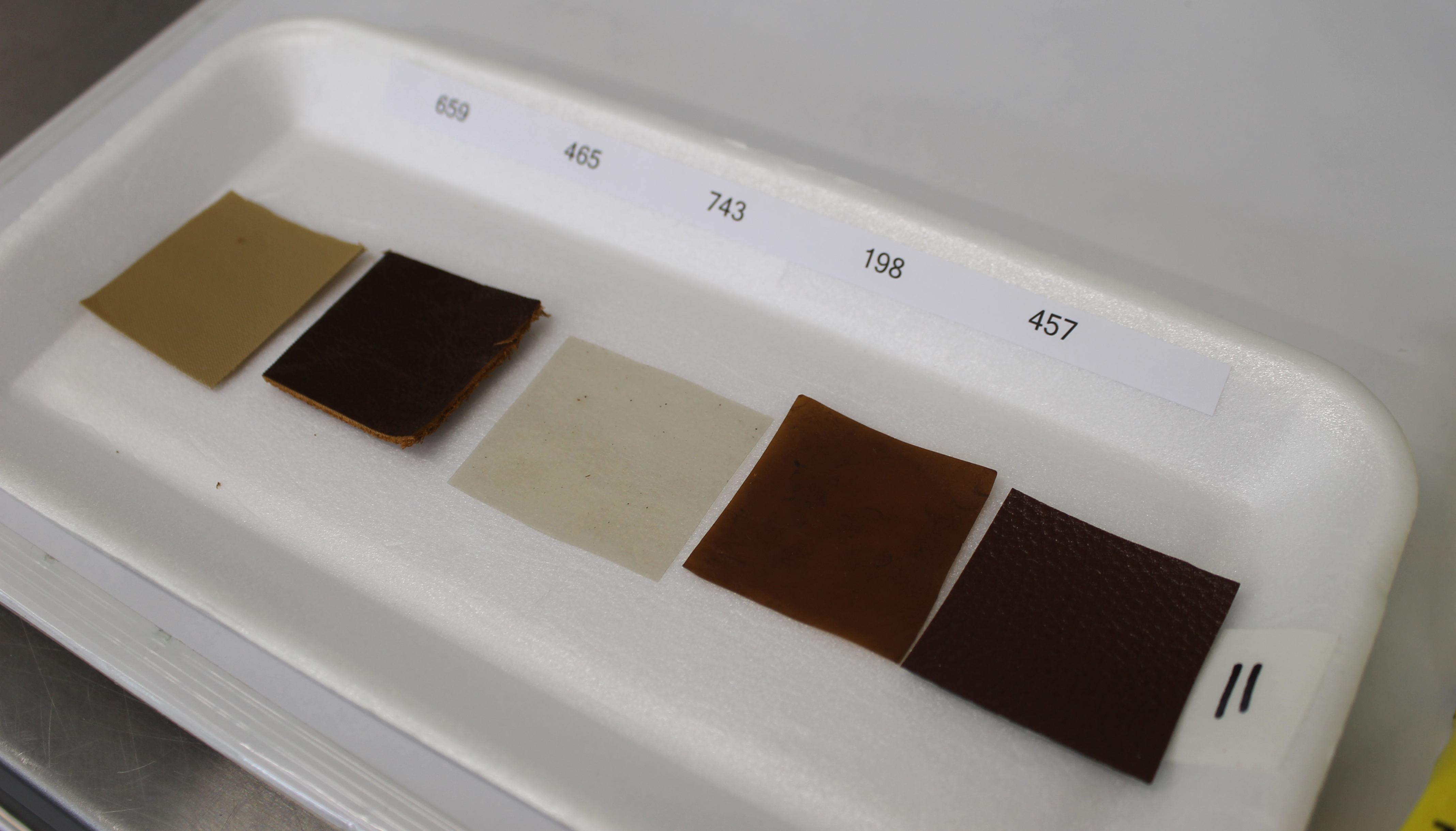
Samples of the new textile made from Kambucha. Photo: Leonie Bolleurs
She states that according to their knowledge, the bacterial cellulose has not yet been grown in South Africa or Africa. However, it has been extensively researched in America and Europe. “There have been several experiments to make biodegradable packaging, facial masks in the cosmetics industry, sausage casings, and fruit rolls – and interestingly enough – it can even be enjoyed as a native Philippine dessert known as nata de coco. This goes to show how versatile it is,” she says.
Monnapula says there is still plenty of room for improvement and further development before reaching a point where she can introduce her work as a contender in the South African market. For instance, the waterproof capability of the textile is yet to be perfected. “More research is also necessary to enhance its hydrophobic and decreasing its hydrophilic properties.”
She is also of the opinion that further dyeing, using environmentally friendly methods and natural dyes to obtain a wider variety of colours, is necessary.
Penetrating the market
Once it is ready, this textile will be a marketable product that can be manufactured for commercial use. “A few European start-up companies have recently managed to penetrate the market and introduce apparel made from bacterial cellulose. I believe that upon further development and modifications, we can eventually follow suit,” says Monnapula.
The bacterial cellulose textile was evaluated in the UFS Sensory Lab, a facility mostly used to test food products. Liezl van der Walt, Sensory Lab Manager, states that the Sensory Lab plays a crucial role in determining the consumer acceptance of new products as well as how the product can be improved. She believes that the textile project was just the beginning of many more textile-related sensory panels to take place.
Within the apparel industry, this textile can be used to make products that are typically made of leather, including bags, jackets, shoes, and bucket hats. – Matseliso Monnapula